PUSH FLOWS
Local optimizations
In a push flow system, each resource is optimized localy, regardless to global performance of the whole
system. Generaly, a powerful IT system tries optimizing the usage of each resource and scheduling of each operation.
Let's take a simplified example of a good mood dispenser manufacturing process, at YIPEE Corp.
A central IT system handles material requirements for raw dispenser bases, prepared at subcontractor's facility,
based on forecasts. The forecasts never show accurate, despite the use of the latest version of SNIF®, from GUESS software.
Raw bases are prepared by an operator obssesed by the swift handling of his chore, meaning preparing the raw
(grey ) bases dwelling in front of his workbench.
He's even more obsessed by the perspective of a nice bonus related to his achievement, over the standard.
As his area is quickly jammed, he pushes the batches of finished bases (red)
to the buffer in front of next operation, assembly.
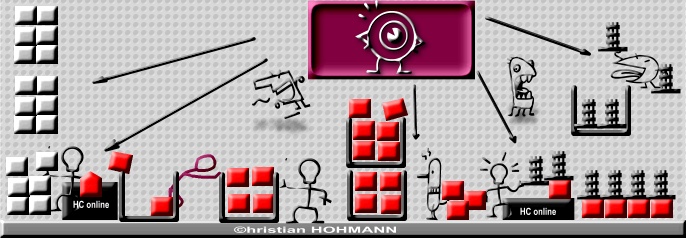
Assembly is saturated with
finished bases
arriving faster than assembly pace. This inventory is known by the central IT system, yet inventory has to be counted
regularly to insure physical quantities match the virtual inventory data, which is not a given.
Central IT analyzes assembly yield is under the computed optimum, so the operator never got a bonus.
The high tech Mood generator is the core component of the dispenser, mounted onto the base at assembly.
Mood generators are manufactured on an other line. Even generators production pace is sufficient for feeding assembly,
the shop manager (obviously not using this fabulous product!) stresses his team to produce more,
as his productivity indicator de (computed by central system) shows performance under expected level.
As a matter of fact, nobody ever gets a bonus in this team.
Finsihed products pile up at warehouse, waiting for customers orders.
10% stay long enough to rust, units to discard as they cannot be recycled.
Note: dispensers come in only one color, namely
red, relaxing color YIPEE marketing
specialists say.
PULL FLOW
Global Optimization
YIPEE Corp reorganizes its production to pull flow, limiting inventories to minimum.
There is no more search for local optimisation of resources, but consistently to theory of constraints (TOC)
tries to optimize globally.
The new performance indicator is now service rate. It is equal to:
number of compliant ontime deliveries (at correct location) / total number of deliveries
IT system is limited to raw material, parts and bases ordering, plus shipment to customers management.
Work posts communicate directly via kanban cards.
Operators have been trained about kanban principles and have been instructed to produce only
what is required, via kanban cards.
Management of the different workshops are dispatched to other jobs, a coach and not longueur a boss
takes care about dispenser line.
Assembly feeds a limited inventory. Each time a dispenser is delivered to a client, the associated kanban
is transmited to assembly, notifying the need to compensate the sold unit in the inventory. When assembly
delivers the new dispenser, kanban is attached.
Assembly takes one
finished base
from finished base inventory and one mood generator from generator inventory. The kanban attached to
finished base
is sent to base preparation,
while kanban previously attached on generator is sent back to generator manufacturing cell.
Operator manufacturing generators waits until a kanban is sent before manufacturing a new unit.
Without kanban, no production. He is eventually dispatched to another department if his load at generators does not fill
his day.
Base preparation operator is just replacing one in the
finished base buffer attaching the
kanban which triggered this order. An other base is to be fixed, as a waiting
BLUE
kanban shows in the upper case.
The raw bases
can't be kanban ordered yet (supplier is not able to organize his process that way), they keep batch ordered, yet
batch sizes are reduced, compared to previous situation.
|
|
The author, Chris HOHMANN, is partner
in an international consulting firm.
He advises companies on industrial and logistics performance issues.
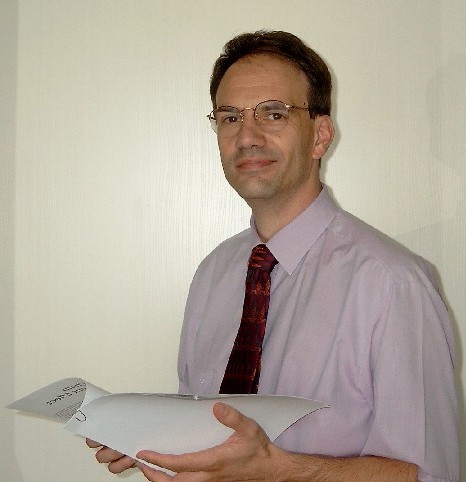
Contact the author
|
TOC assumption
The sum of the local optima (or local efficiencies)
does not produce the system optimum.
|
The process described in this example is fitted with three kanban loops:
- Finished dispensers loop
- Base loop
- Generators loop
|
|
What happened to bonuses?
Customer satisfaction, measured by service rate, is now the global perfomance indicator. Workers
have less stress and a nearly perfect visibility about their own customer (next step) demand.
Workers first question will be: so what about bonuses?
Yield related bonuses don't make any sense in this new system, as producing over the required quantity is contrary to the
new rules and would only push more goods to the different inventories.
Two approaches are possibles:
Keep a variable part in wages, giving bonus to everybody, directely proportional to service rate.
Suppress the variable part and integer bonuses into wages.
| |
Both cases are favorable to operators:
Base preparing chap keeps his wages complement brought by his bonus (while sweating less), the
others, never envoying bonuses will get a reward for their efforts from now on.
The company pays the bonuses with the savings made on inventory carry over expenses
(financial costs, real estate, gards, obsolescence, etc.) |
Even better pulled flows
Customer can choose color!
In order to satisfy even more its clients, and thanks to first success, YEPEE corp
decided to propose its marvelous good mood dispensers in six colors:
Tonic Yellow |
Optimistic Pink |
Spring Blue |
Bright Red |
Deep Blue |
Prairie green |
A finished dispenser inventory is set at shipping department.
For keeping our example, simple, inventory is set to one piece in each color.
Each dispenser has its kanban, in same color as the base, for easy identification.
After each shipment / sale,
(1)
the kanban of the sold unit is send (yellow arrow) to assembly.
For assembly, this means "replenish the inventory with one unit in the same color as kanban".
In our case, sold dispenser is red.
Assembly operator
(2)
gets a generator out of generators buffer and sends (yellow arrow) kanban to base preparation
(3).

Operator at base preparation
(3) gets one
raw base
and prepares in desired color, red in our example. The
raw bases are not kanban managed, but an
(orange)
marker card indicates the minimum stock. As soon as the orange marker card becomes appearent, it must be sent
(yellow arrow) to supplier (or purchasing dep.) to get a new batch of bases from supplier.
Operator in charge of generators
(4)
prepares a new generator each time a location in finished generators is empty, which is a visual signal for him to
compensate consumption. This way is not realy kanban (as there is no card), but principle is same:
- Empty location = manufacture
- No empty location = do not manufacture
Buffer size (2 in our example) is sufficient to cover a new request occuring while operator manufactures one unit.
|
This diagram describes physical flows (black arrows) and information flows (yellow arrows).
Value Stream Mapping (VSM), basic tool of
lean manufacturing is used for current situation drawing, analysis and process reengineering
using this approach.
|
|
This page was brought to you by ©hris HOHMANN - http://chohmann.free.fr/
|