FLUX POUSSES
Optimisations locales
Dans un système à flux poussés, chaque ressource est optimisée localement, indépendemment de la
performance globale du système. En général, un puissant système informatique tente d'optimiser à la fois l'usage de
chaque ressource et d'ordonnancer au mieux chaque opération.
Prenons l'exemple simplifié d'une fabrication de diffuseurs de bonne humeur de la société YOUPI.
Le système central lance les approvisionnements de culasses sur prévisions. Les prévisions ne se réalisent jamais,
alors que le système est doté de la dernière version du programme SNIF® d'OPIF software.
Le préparateur de culasses est obsédé par le traitement des culasses
(grises ) en attente devant son poste,
d'autant qu'il perçoit une substantielle prime s'il réalise une production supérieure au standard.
Son poste s'engorgeant rapidement, il pousse le stock de culasses terminées
(rouges) vers le poste
suivant.
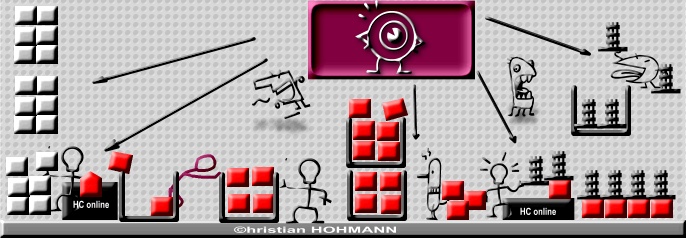
L'assemblage est saturé de
culasses terminées
qui arrivent plus vite qu'il ne peut les assembler. Ce stock est néanmoins connu du système central, mais il faut le
recompter régulièrement pour s'assurer que les quantités physiques correspondent au stock théorique,
ce qui n'est pas évident. Le système central analyse que le rendement à l'assemblage est sous l'optimum.
L'opérateur ne reçoit jamais de prime.
Le générateur d'humeur est l'autre composant du diffuseur monté sur la culasse à l'assemblage.
Il est fabriqué par une autre ligne. Bien que le rythme de production soit suffisant pour le montage, le chef d'atelier
"générateur" (qui de toute évidence n'utilise pas ce fabuleux produit !) pousse son équipe à produire davantage,
car son indicateur de productivité (calculé par le système central) montre que leur performance est trop faible.
Du coup personne dans cette équipe ne reçoit de prime.
Les produits terminés s'entassent au magasin de stockage, attendant que les clients les commandent.
10% restent suffisamment longtemps pour rouiller, il faut alors les jeter, car ils sont irrécupérables.
Notons que les diffuseurs n'existent, au moment de leur lancement sur le marché, qu'en finition
rouge, couleur appaisante disent les
spécialistes du marketing de chez YOUPI.
FLUX TIRES
Optimisation globale
La société YOUPI réorganise sa production en flux tirés et limite les stocks au minimum.
Elle ne cherche plus à optimiser localement l'emploi de ses ressources, mais conformément à la devise de la
théorie des contraintes (TOC) s'attache à optimiser globalement le processus.
Le nouvel indicateur de performance est le taux de service. Il est égal à :
nombre de livraisons conformes et à l'heure (et au bon endroit) / nombre total de livraisons
Le système informatique ne sert plus qu'à commander les matières premières, pièces et culasses, ainsi qu'à gérer les
expéditions vers les clients. Les postes communiquent directement entre eux à l'aide de kanbans.
Les opérateurs sont formés au principe du kanban et ne doivent produire que ce qui est effectivement demandé, via les kanbans.
La hiérarchie des différents ateliers est réaffectée, un animateur et non plus un chef s'occupe désormais de la ligne diffuseurs.
Le poste d'assemblage alimente un stock réduit. Chaque fois qu'un diffuseur est sorti du stock pour être livré au
client, le kanban associé au diffuseur est transmis à l'assemblage, lui indiquant ainsi qui'il faut compenser l'unité
vendue dans le stock. Lorsque l'assemblage livre son diffuseur, il lui attache le kanban.
L'assemblage prélève une
culasse terminée
du stock culasses et un générateur d'humeur du stock générateurs. Le kanban de la
culasse terminée est transmis au poste
de préparation des culasses, tandis que le kanban fixé sur le générateur est transmis au poste de fabrication des générateurs.
L'opérateur fabricant les générateurs attend qu'on lui transmette un kanban avant de se mettre à fabriquer un générateur.
Sans kanban, pas de fabrication. Il est éventuellement affecté à d'autres tâches si le rythme des fabrications ne permet
pas de l'occuper durant une partie raisonnable de la journée.
Le préparateur de culasses est en train d'en remettre une dans son stock de
culasse terminée en lui attachant le
kanban qui a déclenché cette commande. Une autre culasse est à préparer, comme le montre le kanban
BLEU sans produit dans le casier du haut.
Les culasses brutes
ne peuvent être commandées par kanban (le fournisseur n'étant pas capable de s'organiser pour cela),
elles sont commandées par lot, mais les tailles des lots sont plus réduits que précédemment.
Que sont devenues les primes ?
L'objectif global étant la satisfaction du client, mesuré par le taux de service, les opérateurs
travaillent désormais avec moins de stress et une parfaite visibilité de la demande de leur propre client
(le poste suivant).
La question légitime des opérateurs est : que deviennent les primes ?
Les primes de rendement n'ont plus aucun sens, car produire au-delà de la demande est contraire
aux nouvelles règles et ne bénéficierait qu'au gonflement des différents stocks.
Deux approches sont possibles :
Garder une part variable en attribuant une prime à tous, qui est directement proportionnelle au taux de service.
Supprimer la part variable et intégrer les primes dans le salaire.
| |
Les deux cas sont favorables aux opérateurs :
Celui des culasses conserve le complément de salaire
apporté par sa prime (tout en transpirant moins), les autres qui n'en touchaient jamais en perçoivent désormais.
L'entreprise finance ces primes par les économies sur les frais précédemment liés aux stocks
(frais financiers, gardiennage, perte par obsolescence, etc.) |
Flux encore mieux tirés
Le client a le choix de la couleur !
Pour mieux satisfaire ses clients et fort des succès de ses premiers efforts, la société YOUPI
décide d'offrir ses merveilleux diffuseurs de bonne humeur en six couleurs :
Jaune tonic |
Rose optimiste |
Bleu printemps |
Rouge éclatant |
Bleu profond |
Vert prairie |
Un stock de diffuseurs terminés est mis en place à l'expédition.
Pour la clarté de notre exemple, le stock est dimensionné à une pièce par couleur.
Chaque diffuseur est muni de son kanban, de couleur identique à la culasse, pour l'identifier.
A chaque vente, le kanban de l'unité vendue est transmis (flèche jaune) au poste d'assemblage
(1)
Pour ce poste, cela signifie "recomplète le stock d'une unité dans la couleur du kanban".
Dans notre cas, le diffuseur vendu est rouge.
L'opérateur d'assemblage
(2)
prélève un générateur du stock générateurs et transmet (flèche jaune) le kanban au poste finition culasse
(3).
prend une
culasse brute et la prépare dans la
couleur désirée, rouge pour notre exemple. Les culasses
brutes ne sont pas gérées par kanban, mais une fiche
(orange)
marque le stock minimum. Dès que la fiche
orange devient apparente, il faut la transmettre (flèche jaune) au fournisseur (ou au service approvisionnement) pour
qu'il envoie un nouveau lot de culasses.
L'opérateur chargé des générateurs
(4)
prépare un nouveau générateur chaque fois qu'un emplacement
dans le stock de générateurs terminés est libre, signal visuel pour lui de compenser la consommation. Cette façon
de procéder n'est pas à proprement parler du kanban (il n'y a pas d'étiquette), mais le fonctionnement est identique :
- emplacement libre = fabriquer
- pas d'emplacement disponible = ne pas fabriquer
Le dimensionnement de son stock (2 dans notre exemple) est suffisant pour couvrir une nouvelle demande pendant que
l'opérateur refabrique une unité.
|
L'auteur, Christian HOHMANN, est directeur associé en charge du pôle
Lean et Supply Chain
au sein d'un cabinet international.
Ses équipes interviennent en conseil sur des problématiques
de performance industrielle et logistique.

Contacter l'auteur
|
Devise de la TOC
La somme des optima locaux n'est pas égale à l'optimum global.
|
Pour celles et ceux qui ne comprendraient pas les concepts expliqués dans cette page :
Le système décrit en exemple est pourvu de trois boucles kanban :
- la boucle des diffuseurs terminés
- la boucle des culasses
- la boucle des générateurs
|
En général on s'arrange pour que l'opérateur voit le supermarché
et puisse prendre les décisions à vue.
|
Aller au
Supermarché
Le schéma décrit les flux physiques (flèches noires) et les flux d'informations (flèches jaune).
Le Value Stream Mapping (VSM) ou cartographie de la valeur, outil de base du
lean manufacturing est une technique de
représentation, d'analyse et de reconstruction des processus qui utilise cette approche.
|
|
|
|