L'analyse PM (Physique-Mécanique ou Phénomène-Mécanisme) est une méthodologie développée pour
éradiquer les problèmes récurrents de faible occurrence ou encore les causes de micro-arrêts dans un déploiement de la
TPM.
Ce type de problème est généralement traité tardivement, du fait de leur faible impact au regard
d'autres causes prépondérantes, et difficile à traiter car les causes sont complexes, subtiles et de multiples causes
interagissent. L'approche causes-effet est habituellement insuffisante pour en venir à bout.
L'analyse PM est une démarche structurée en 8 étapes servant à identifier et investiguer de manière
exhaustive les facteurs et causes probables d'un problème. Les quatre premières étapes isolent et identifient les
causes racines des dysfonctionnements. Les quatre étapes suivantes mettent les facteurs influents sous contrôle.
Etape | Contenu |
1. Etudier le phénomène |
Définir et décrire clairement le phénomène pour mieux le cerner et le comprendre. Cette étape s'attache
à rassembler des éléments factuels, afin de ne pas se complaire dans les théories. |
2. Isoler les principes physiques |
Expliciter le phénomène en fonction des principes physiques mis en oeuvre et non de croyances et intuitions. |
3. Comprendre les conditions d'apparition |
Rechercher les conditions qui favorisant et/ou produisant les dysfonctionnements, toujours basés sur les
principes physiques. Il s'agit d'être exhaustif car la persistence des dysfonctionnements est souvent due à
un traitement partiel des causes, des mesures correctives incomplètes. |
4. Discriminer les facteurs déclenchants par l'analyse causale |
Rechercher les facteurs selon les 5M : Machine,
Matière, Modes opératoires (ou Méthodes), Main d'oeuvre, éventuellement Milieu
qui créent les conditions d'apparition des dysfonctionnements. |
5. Définir les conditions optimales (Valeurs Standard) |
Il s'agit de définir un état idéal dans lequel les conditions d'apparition (étape 3) ne peuvent se
produire. Cela peut impliquer la qualité de la matière ou des réglages, la précision ou la variabilité des alignements,
l'usure ou les conditions d'utilisation, par exemple. |
6. Recueil de données de mesure |
Définir les moyens d'identifier les micro - arrêts, les mesurer pour pouvoir mener le travail
d'investigation. Ensuite on se donne une période pour relever les données, qui doivent être statistiquement significatives.
Le relevé étant confié au personnel de terrain, il faut que les mmoyens déployés soient suffisamment simples, pragmatiques
mais néanmoins précis. |
7. Déterminer les dysfonctionnements à traiter |
A partir de cette étape, on revient aux basiques de la résolution de problèmes, consistant à prioriser
le traitement des causes en fonction de paramètres tels que gravité, durée du dysfonctionnement, impact, etc.
de proposer les actions correctives, les mettre en place, suivre les résultats. |
8. Proposer un plan d'action puis le mettre en oeuvre |
|
|
Au travers de cette analyse, les membres du groupe de travail apprennent à connaître le fonctionnement
intime des machines, ce qui est un moyen d'élever leur niveau de connaissance et de compétence.
La clé de l'analyse P-M est la compréhension des principes physiques mis en oeuvre et des facteurs
concourrant aux dysfonctionnements.
|
L'auteur, Christian HOHMANN, est directeur associé
au sein d'un cabinet spécialisé.
Il intervient en conseil sur des problématiques
de performance industrielle et logistique.
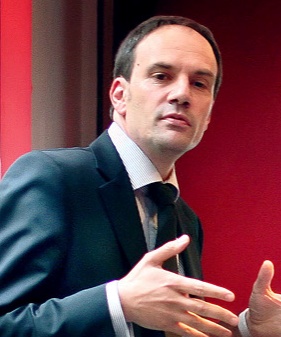
Contact commercial
|
|